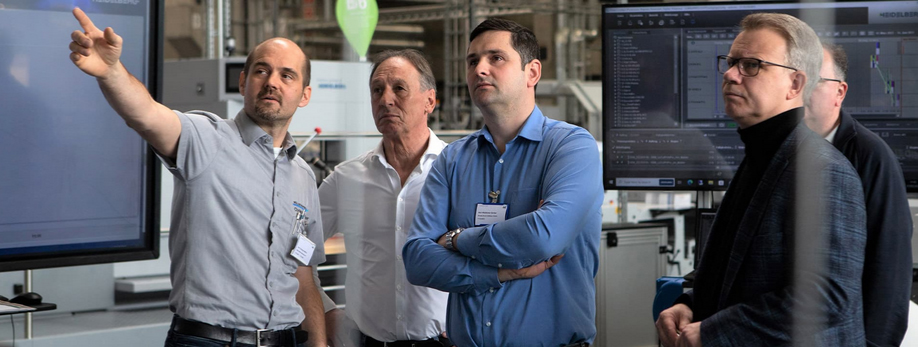
The integration of prepress data is also becoming increasingly important in saddle stitching. That’s why we recently connected the Primera PRO to Heidelberg’s Prinect workflow system in the showroom of the Heidelberg Print Media Center in Wiesloch, Germany. This enables us to demonstrate the entire production workflow from print to end-product even more impressively for interested customers.
Anyone who talks about a workflow system from prepress to press and postpress – for example the Connex developed by Muller Martini – today primarily thinks of the efficient, fully automated and barcode-controlled production of digitally printed short (or long) runs. However, it is easy to forget that the integration of prepress data is also becoming increasingly important in saddle stitching, where the number of conventionally printed sheets is usually much higher. The aim is to not only reduce manual intervention and thus avoid errors, but production can also be tracked in detail and subsequent jobs can be optimized. Because at the end of the day, only one thing counts in saddle stitching as well: productivity.
It makes little sense to enter data twice
It is often the case that a customer already has a Management Information System for prepress – i.e. for planning and costing print jobs. Therefore, it makes sense to link this MIS as the “digital brain” of the company to the saddle stitcher. True to the motto: “If the data is already there, we want to (re)use it.”
It makes little sense to enter the data twice – first into the prepress system and then into the press. That’s because you lose time, for one thing, and it’s also a potential source of errors. A founding member of the CIP4 consortium over two decades ago, we at Muller Martini have always been at the forefront of data integration in machines using JDF and JMF standards.
Less effort for the machine operator
When printers with an associated bindery in Europe have recently implemented such a workflow solution, it is often because some countries and the European Union provide funding for technological developments. A prime example of a workflow quantum leap is Connex LineControl Finishing, which enables Muller Martini equipment to be integrated into a higher-level planning system via a digital job folder (JDF). All relevant production control data is taken from the JDF file, prepared for the connected production line and then transferred to the production line.
This enormously reduces the organizational effort that the machine operator has to make in his daily work. Job data such as run length, job name or format are available directly at the machine without manual input, which ensures data quality throughout the entire production process. Additionally, Connex LineControl Finishing offers the possibility to integrate barcode scanners for job activation and defect detection.
Via Connex LineControl Finishing – which it takes to act as a link or “translator” between MIS and machines – any customer’s workflow system can in principle be connected to our Prinova and Primera PRO saddle stitchers.
Young people love IT-savvy solutions
Our Primera series, launched in 2008, could already be connected to an MIS. If, over the years, more and more graphic companies decided to use it, it was partly due to the advantages mentioned above. On the other hand, it also has to do with the fact that younger press operators are more IT-savvy and thus more amenable to automated (workflow) systems. In this context, I well remember an apt statement made by Sven Regen, co-owner and Managing Director of PIEREG Druckcenter Berlin GmbH, when he invested in a Prinova two years ago: “Against the background of today’s shortage of skilled workers, it is important for an employer to inspire young people with state-of-the-art technology.”
The Primera PRO in Muller Martini’s Print Finishing Center is also JDF-controlled. However, since we “only” saddle stitch here in Zofingen and do not print, the file does not come from the Prinect prepress system.
The Primera PRO in Wiesloch…
In addition to the Print Finishing Center, we have been using a Primera PRO in another showroom for the past two years – namely the Heidelberg Print Media Center in Wiesloch, Germany, where, in addition to customer demos, the Heidelberg Technology Days take place twice a year. This is a classic win-win situation for our two companies, which are linked by a partnership. Heidelberg can demonstrate end-to-end applications, including postpress, to its customers and produce proprietary brochures on them – including brochures for its presses.
Muller Martini, in turn, can show interested customers the entire production workflow from print to end product with its extensive Primera PRO line – cover feeder, four flat pile feeders and two vertical feeders, SEMKO, 0504 three-knife trimmer with center cut, Perfetto stacker with Amrys and delivery table. With “Elemanta Animal Guide” (A5+) and “Living Culture” (A4), we have two standard demonstration products with which we can optimally demonstrate format changes.
…is now linked with Prinect
In Wiesloch, we also offer combined Heidelberg/Müller Martini customer demonstrations with our service technicians and instructors. In addition, for two months now, these have been made even more attractive by the addition of a technological component. Since mid-March, the Primera PRO in Wiesloch has been connected to the Prinect workflow system from Heidelberg. Anyone who comes to the Heidelberg showroom for a complete demo can therefore see not only the mechanical components of our saddle stitcher, but also the entire data flow through all the machines – and can tell at a glance whether a production run was good or not.
Even the first Prinect/Primera PRO customer demonstration for Strube Druck & Medien GmbH, which I personally accompanied, was a complete success. Actually, the German company from Felsberg was in Wiesloch primarily for printing and folding machines. However, they asked to have a look at the Primera PRO for 30 minutes as well. Instead of half an hour, the demo ended up lasting an hour and a half due to the customer’s great interest. Waldemar Gerber, Postpress Shift Manager at Strube, was visibly surprised and could hardly believe that we had integrated the saddle stitcher into Prinect. He was particularly impressed by the short changeover times.
After the appetizer, the in-depth talks
Next time, Strube will also be coming to the Print Finishing Center with a larger delegation to take a closer look at the Primera PRO together with our technicians and also to take a look at the numerous other solutions from the Muller Martini portfolio. Strube is a good example of how our Primera PRO in Wiesloch acts as an initial appetizer for customers, who later stop by in Zofingen if they want to learn more about our saddle stitcher.
Do you also want to know more about our Primera PRO and its connection to Prinect or to another workflow system? Then feel free to contact me – I’ll be happy to answer your questions!
Yours,
Christoph Müller,
Head of Muller Martini Print Finishing Center
This text is reproduced with kind permission of Müller Martini, you can read the original article first published here